How Call Solutions Eliminate Bottlenecks on the Factory Floor
Inefficiency on the factory floor can cost industries millions each year. Studies show that up to 20% of productive time is lost due to communication failures and maintenance delays. Additionally, the average machine downtime can range from 15 to 30 minutes per failure, directly impacting productivity and revenue. If we consider that an automotive production line, for example, manufactures a car every 3 minutes, a simple stop can represent thousands of dollars in losses in just a few hours.
Another relevant data point: a survey from the Lean Enterprise Institute shows that 65% of production problems are caused by delays in decision-making and slow response times to resolve failures. These bottlenecks create a domino effect, reducing operational efficiency and increasing production costs.
In light of this scenario, companies are adopting smart call solutions to streamline processes and minimize losses. Smart Call Anywhere from DESTEC Solutions is one of these innovative technologies transforming the factory floor, improving communication and enabling accurate tracking of operations.
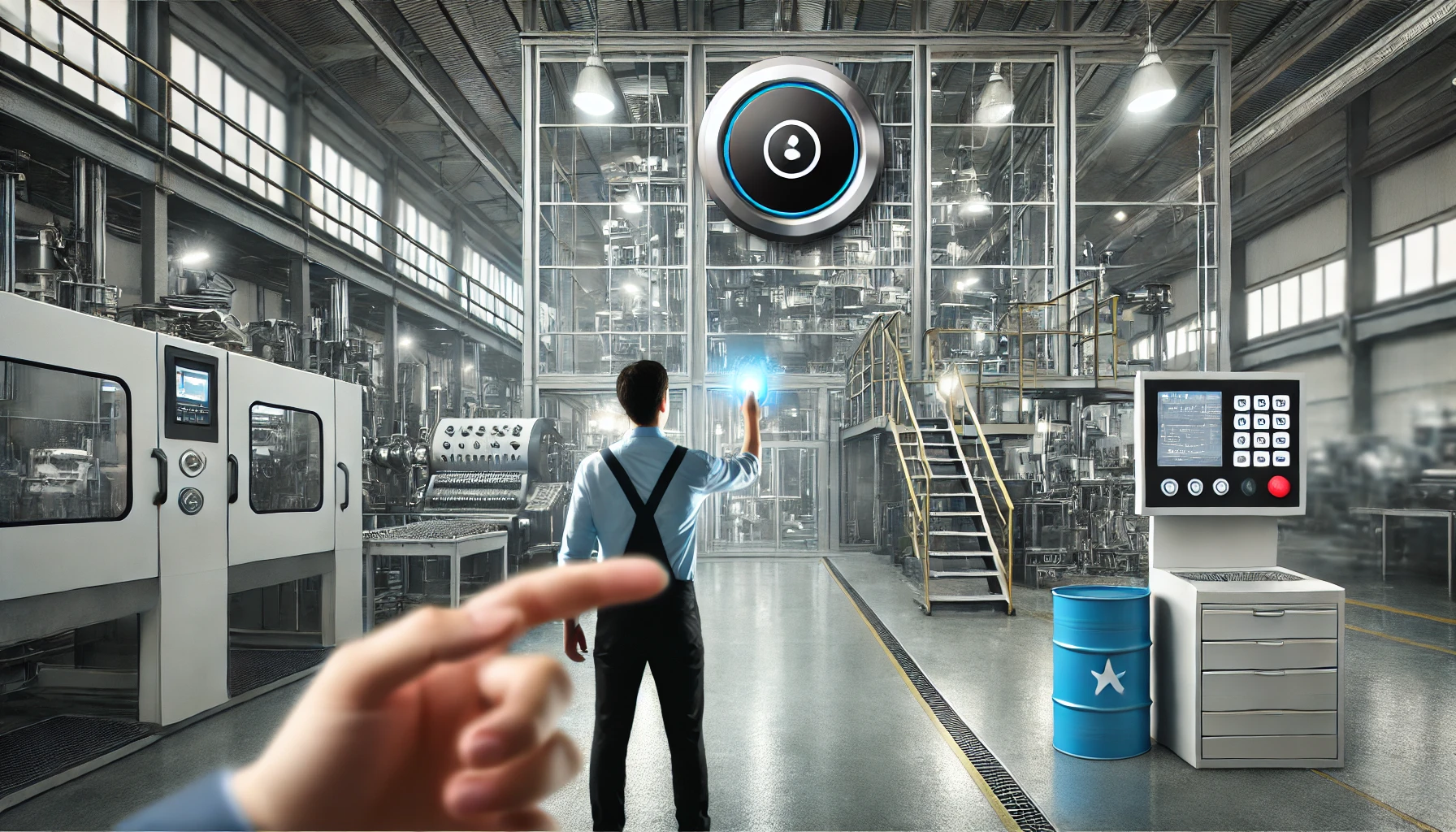
The Main Bottlenecks on the Factory Floor
Before we understand how technology can help, it’s essential to know the main challenges factories face:
Slow Response Time for Maintenance and Support
When a machine stops, operators need to locate a technician manually, which can delay production restart.
Impact: Reduced production capacity and lost revenue.
Lack of Agility in Communication
Production operators face difficulties in requesting assistance from different departments like quality, logistics, and engineering.
Impact: Build-up of work-in-progress products and increased production cycle time.
Inefficient Inventory and Internal Logistics Management
Without an efficient system, operators may lose time waiting for material replenishment or removal of finished products.
Impact: Delays in order delivery and increased operational costs.
Lack of Tracking and Data Analysis
Without precise metrics, managers can’t evaluate where the main problems and bottlenecks are.
Impact: Difficulty in implementing continuous improvements and reducing waste.
Call Solutions: How They Eliminate Bottlenecks
With the implementation of Smart Call Anywhere, gyms can improve operational management, reduce costs, and increase member satisfaction.
How does it work?
✅ Strategically placed call buttons in the gym, allowing members to request service without having to look for instructors.
✅ Real-time notifications for the team, avoiding unnecessary movement and optimizing staff distribution.
✅ Maintenance control via IoT, reducing the time equipment is out of service and improving the lifespan of machines.
✅ Monitoring via Bell Cloud, allowing managers to track operational metrics and adjust staffing based on demand.
The Benefits: How Technology Is Reducing Costs in Gym
Smart Call Anywhere offers an intelligent platform that integrates agile communication and real-time data collection. Here’s how the solution works in practice:
Reducing Downtime: Faster Maintenance
In many factories, when a machine breaks down, the operator has to leave their workstation to find a technician, causing lost time. With Smart Call Anywhere, simply pressing a button or scanning a QR code immediately activates the maintenance team.
Benefits:
- Reduced mean time to repair (MTTR).
- Automatic recording of response and execution times.
- Increased equipment availability.
Success Story: The implementation of Smart Call Anywhere reduced downtime by 50% on the production line of a major automotive manufacturer, resulting in greater efficiency and less production loss.
Fast and Efficient Communication Between Teams
Efficient communication between departments like production, quality, logistics, and engineering is crucial. Smart Call Anywhere allows operators to request support instantly via buttons, keypads, or QR codes.
Benefits:
- Reduced wait times for assistance.
- Avoids unnecessary movement on the factory floor.
- Ability to automatically escalate calls.
Practical Example: If an operator identifies a quality issue, they can immediately notify the inspector without interrupting production. The call reaches the inspector via a smartwatch or interactive screen, speeding up problem resolution.
Efficiency in Inventory and Logistics Management
Delays in raw material replenishment and finished product removal are common challenges. With DESTEC Solutions’ solution, operators can quickly request material transportation without leaving their station.
Benefits:
- Improved material flow within the factory.
- Reduced wait times for moving loads.
- Better organization of the internal supply chain.
Application: Operators can request a forklift to remove pallets just by pressing a button, ensuring production line space is optimized.
Data Analysis and Smart Monitoring
Bell Cloud, DESTEC Solutions’ intelligence platform, collects data on every call made in the factory. Managers can access detailed information via the IoT portal, tracking metrics such as:
- Mean response time.
- Frequency of calls per department.
- Main reasons for requesting assistance.
Benefits:
- Identifying critical and recurring points in the production process.
- Better predictive maintenance planning.
- Data-driven decision-making to optimize operations.
Why Implement Smart Call Anywhere in Your Industry
The benefits of Smart Call Anywhere go beyond simple communication. The solution directly impacts productivity, operational costs, and factory efficiency.
Competitive Advantages:
- Simple Integration – Works via Wi-Fi, 4G, 5G, or Ethernet, and can be used anywhere in the factory.
- Scalability – Can be implemented in multiple production units and integrated with ERP systems via API.
- Flexibility – Can be used with hardware (buttons and keypads) or QR codes to eliminate the need for physical devices.
Proven Results:
- Full tracking of operations, ensuring visibility and continuous improvement.
- 50% reduction in downtime in large automotive industries.
- Increased operational efficiency with calls directed to the right team.
Conclusion
Bottlenecks on the factory floor can cost millions in operational losses. By implementing Smart Call Anywhere, industries gain agility, efficient communication, and full control over production processes.
If you want to improve productivity and eliminate waste in your production line, DESTEC Solutions’ solution is the ideal choice. Contact us and discover how we can transform your factory! 🚀